About spring thaw, I went looking to buy a loom, and visited a loom dealer that had put a loom aside for me. We ended up sitting in the back of my truck with her poking through a bin of my knitting swatches. She said, "Dang!, These are unbelievable! We need to take these up to the house. You know he was a great knitter."
He pawed through them, and said, " Kinda grubby! No hand spun here!" Thus, was born the hand spun gloves project.
I chose the knitting tools, and sampled hand spun yarns from the stash. No joy. I made up samples of other possible yarns from hand spun singles in the stash.
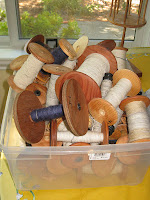
No Joy.
I then took some Rambouillet :
washed it with soap flakes and borax,
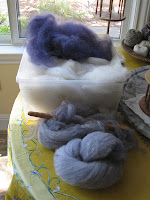
and blended it on my Clems carder with some navy blue combed Romney from a gansey yarn project to produce a lavender color way with white neps for accent. This is my first "art yarn" (neps!). The Rambouillet makes it soft, the Romney gives it good wear at the finger tips. Over all the blend gives reasonable wear without being too harsh.
The bats are sprayed with spinning oil, torn into lengths, and wound on my distaff to facilitate spinning. I spin singles at 4,800 ypp (9s) using the spinning technique shown in videos on this blog,
(
http://gansey.blogspot.com/2012/01/another-video-of-spinning.html )
but with the gang whorls on the flier.
My typical spinning wheel bobbin rotation speed as measured with a digital tachometer is 2,300 rpm. Compare that to the 800 rpm that a stock Ashord Traddy can do. Even with a lace flyer, Ashfords do not go much faster than 1,400 rpm. Most espinners are limited to 1,600 rpm. Twist is DRS controlled to just over 8 tpi. Net spinning rate is around 300 yards per hour. I note that there is nothing on my wheel that a 15th century spinner in Flanders could not have had. I very much doubt if I spin as fast as the spinners in Bruges, 500 years ago. Over all, "spinning" is a tiny part of the project.
I am sure that I do not spin as well as the spinners in Bruges, 500 years ago. They were trained pros with elan.
Singles are wound off onto reels using an electric drill to drive the reel, washed (with shampoo), dried (blocked), and then wound onto smaller plying bobbins. Singles with spinning oil on them need to be washed within a month. Last fall when I was working with hanks of fines, I found wet skeins to be problematic, and moved to washing singles on reels. I made enough reels that I can wash and dry singles faster than I can spin them.
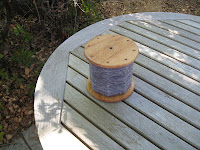
Once the yarn is clean (and loosely wound) on a plying bobbin it can be stored. I have many yarn storage/plying bobbins.
Current plying technique is to put the plying bobbins on a bobbin rack or lazy Kate, feed the singles through my tension box, and ply with the same gang whorl flyer as used to produce the singles. If I was making gansey yarn, I would use the Ashford jumbo flyer so that I could produce knot free, 8 oz hanks. However, the (smaller) high speed flier is much faster and each glove only requires ~2 oz of yarn in 5 pieces, so smaller yarn packages are acceptable.
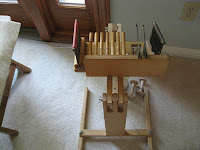
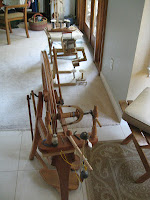
The full plying train of Lazy Kate, Tension Box, and Wheel with high speed flier.
A tension box used on blocked singles really is an advance on Alden's Four Great Principles of Plying. Tension boxes are simple to make, and worth their weight in hand spun yarn.
The finished yarn is wound off the wheel with a cake winder, to produce :
3/4 ounce of 1,500 ypp, 3-ply, glove yarn
(~70 yards)
Knit, the color matches the lavender buds I was putting in the wool bins at the start of the project, and which inspired the color for this yarn. It is warm, durable, and comfortable.
The swaving pricks are the same 1.5 mm used for the cotton sock fabric in the last post. The semi worsted yarn knits easily at 12 to 14 spi. to make an elastic fabric. Yarn for final objects will likely get a final blocking with steam.
Final objects will get washed again.